- O’Band TOP
- 工場見学
工場見学
オーバンドって、一体どうやって作られているの?
工場をのぞいてみると、驚きのノウハウがいっぱい!
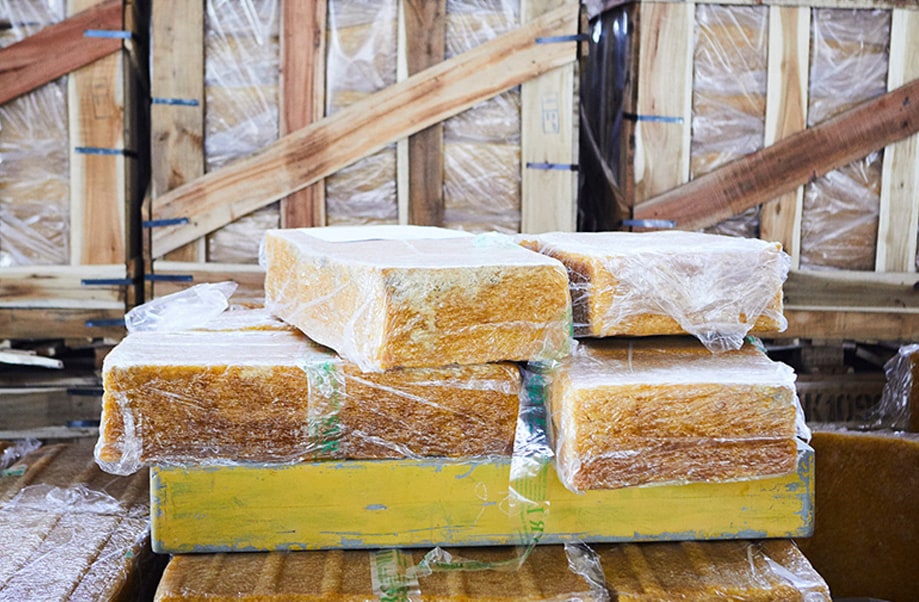
原料となる「生ゴム」が
はるばる海を渡って工場に到着。
オーバンドの原材料として、ゴムの木から採れる樹液を固めた生ゴムが、東南アジアの指定工場から届きます。特に高品質で不純物の少ない生ゴムだけを厳選。ちなみに、これら生ゴムのかたまりは、国際規格で約33.3㎏に統一されています。
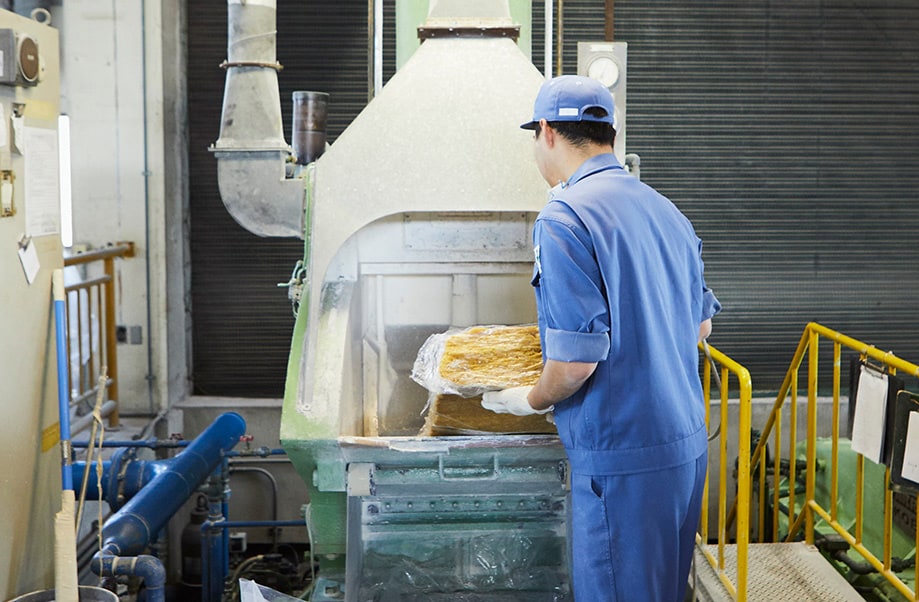
生ゴムと添加剤をブレンド。
押さえながら混ぜてやわらかくします。
次は生ゴムと添加剤を配合する工程です。バンバリーと呼ばれる、2つのミキサーのようなブレードが内蔵された機械で、生ゴムを粉砕しながら配合します。産地によって微妙に生ゴムの性質が違うので、それぞれに合わせた割合で添加剤をブレンドしています。
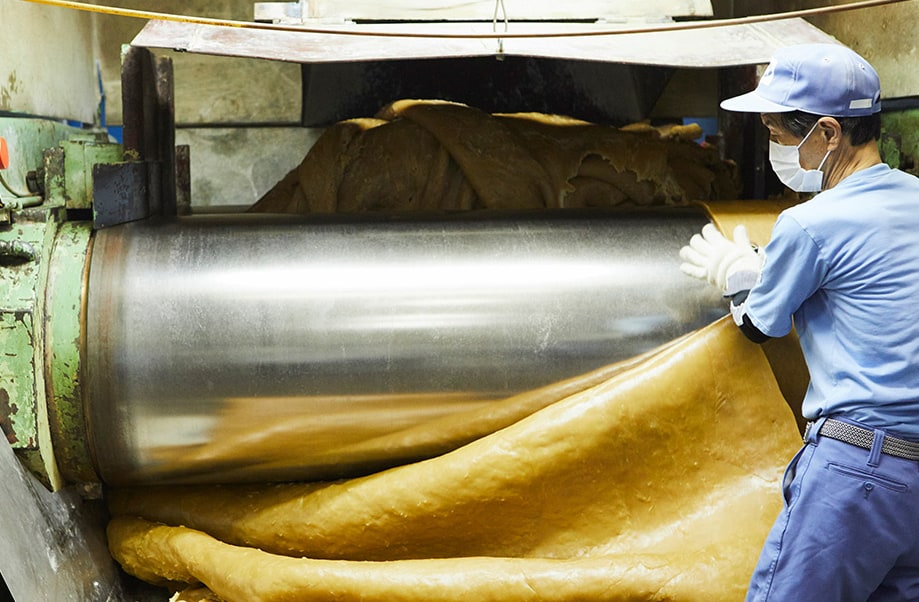
しっかり混ぜ合わせるには練る回数が重要。
繊細な判断は、匠の業!
生ゴムと添加剤をバンバリーで配合した後、さらに大きなローラーで練り上げていきます。この工程を担当するのは、長年の経験を積んだベテランスタッフ。混ぜながら固さを確認することで、あと何回練ればしっかり混ざり合うのかを見極めます。その繊細な判断は、まさに匠のなせる業です。
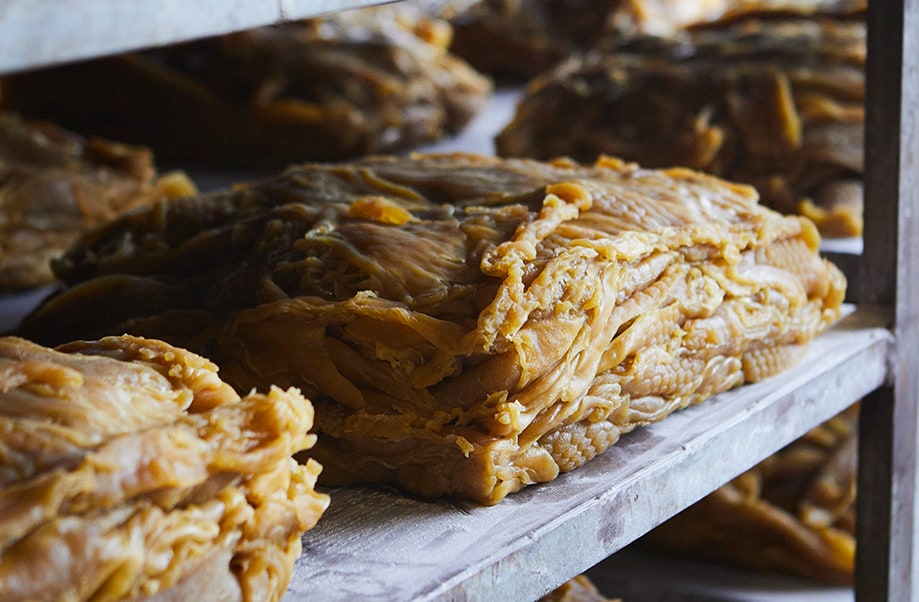
半日以上をかけてじっくりと熟成し、
さらに添加剤をなじませます。
匠によって均一に混ぜ合わせられたゴムは、木クズなどの細かな異物をくまなく取り除かれたうえで、約20kgごとに固められます。そこからは12時間以上の熟成タイム。じっくりと寝かせることで添加剤がしっかりなじむので、気長に待つことが大切です。強く混ぜて寝かせる作業は、パン作りに少し似ているかもしれませんね。
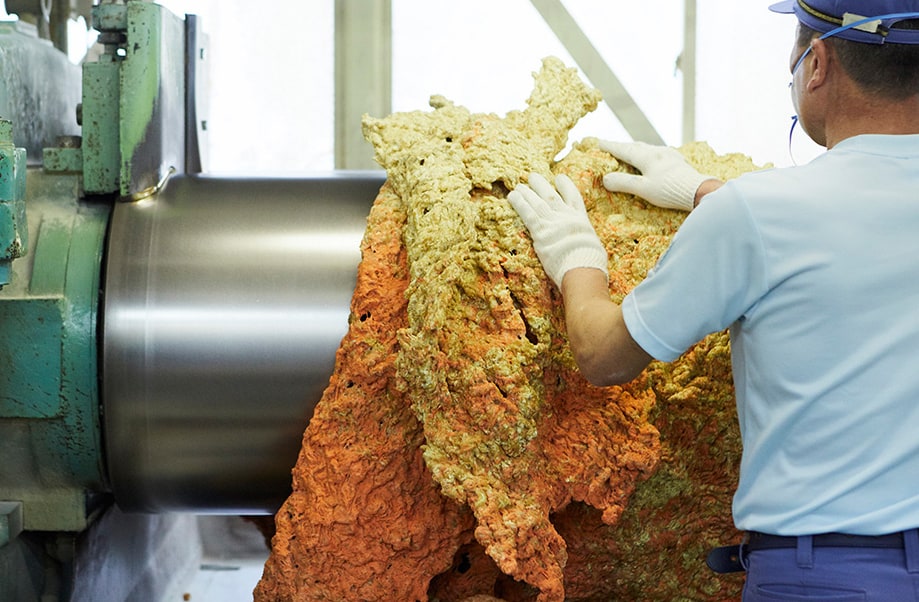
「伸び」と「色」を決める高度な練り作業。
新たな匠の登場です。
熟成が終わると、次の匠のもとへ。温度制御したロールに投入し、伸縮のもととなる硫黄や色素と練り合わせていきます。作業時の気温や湿度、さらには天然ゴムの特性によるバラツキを解消するため、経験と勘で練り時間を調整します。こちらも匠の技が光る、重要な工程です。
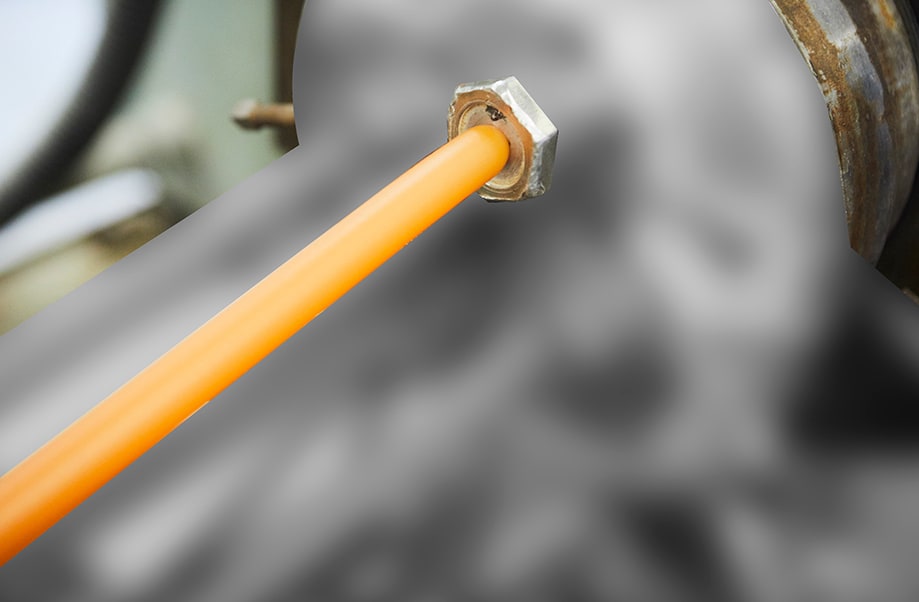
※ぼかしの部分は企業秘密です。
押し出して熱すると… あら不思議!
伸縮性が生まれます。
練り上げられたゴムが冷えて固まってしまう前に、すぐさま次の工程に進みます。ホース状に押し出したあと熱を加えると、よく伸びるキレイな色のゴムに変身。その理由は、熱が加わることで硫黄がゴムに伸縮性を与えてくれるから。さあ、オーバンドの完成まであと少し!
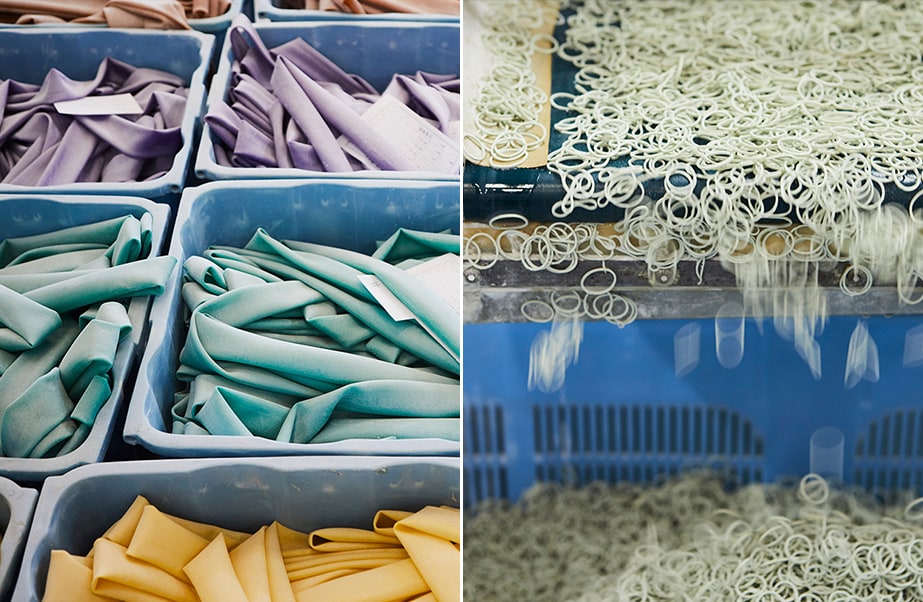
輪切りにすれば、成形の工程は完了!
あとは仕上げを待つのみ。
ホース状のゴムが機械に通され、次々と切断されていきます。出てきたゴムは、もうおなじみの輪っかの姿!「押し出し」の工程で使う金具の型によって輪の大きさや厚みを決め、この「切断」の工程で切る幅を調整することで、さまざまな種類のオーバンドが生まれているのです。
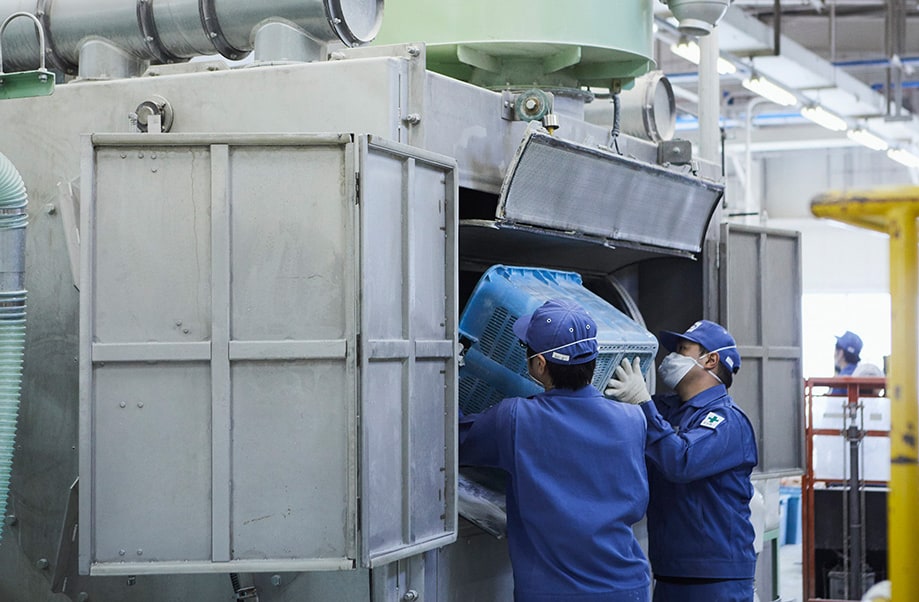
しっかり洗ってすっきり乾かして、
キレイなオーバンドに。
切断が終わるまで、輪っかの内側やゴム同士がくっつかないように、ゴムには打ち粉のような役割をする粉をまぶしています。この粉は最初にお湯で、続いて特殊な洗浄液でキレイに洗い流し、最後に巨大な機械でしっかり乾燥させます。かなりの重さがあるため、持ち上げて投入するのも一苦労!男性二人がかりでの作業です。
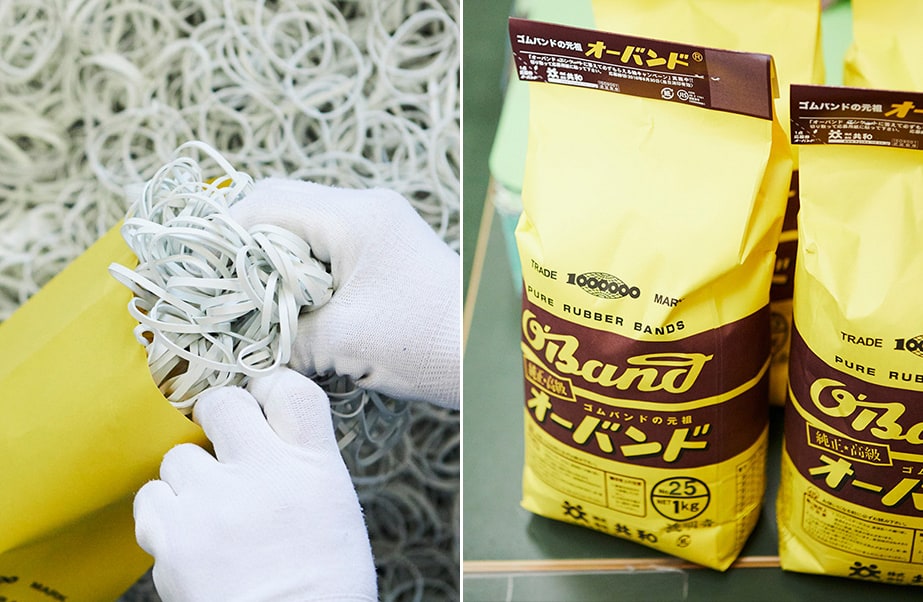
仕上げはひとの手で。
一つひとつ想いを込めて送り出します。
専用の別室でいよいよ袋詰め。異物はないか、違う種類が混ざっていないか、不良品はないか――。厳しく最終チェックをしたあと、量を調整し、手作業でていねいに梱包していきます。「安心してたくさん使ってほしい」、そんな願いを込めたオーバンドを、みなさまの元へと送り出します。
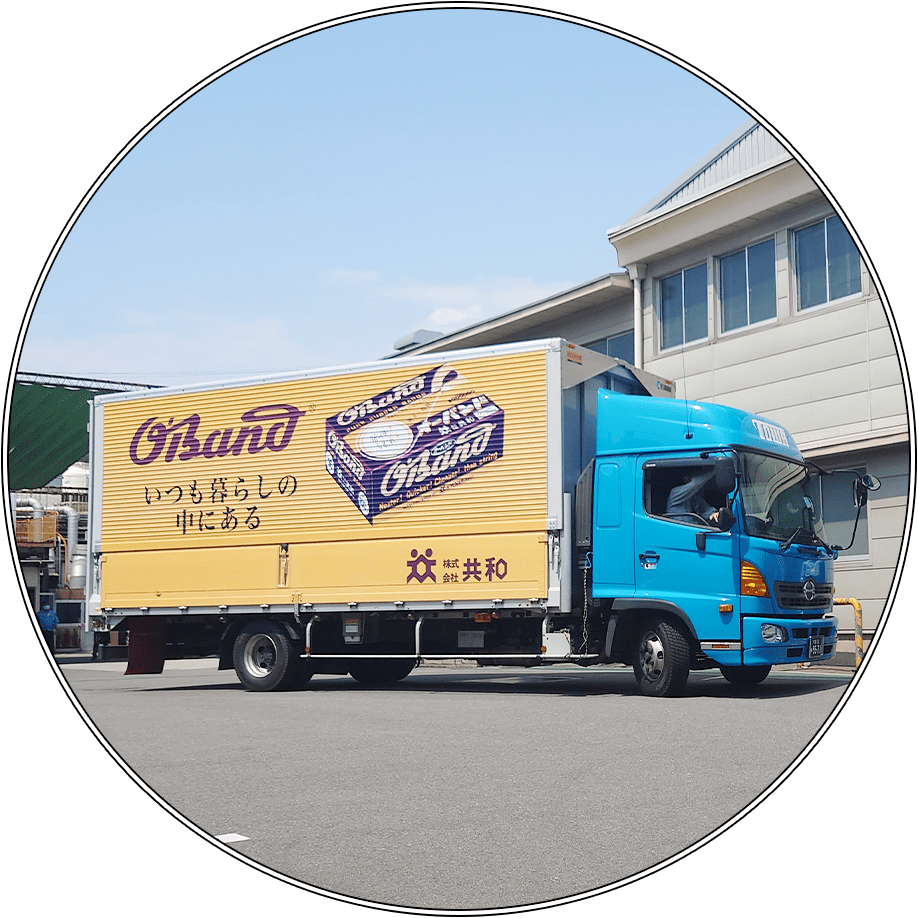